Tom Vroemen (E.22) : Revolutionary lattice

Led by CEO Tom Vroemen (EMBA.22), architectured materials expert Tetmet patented a new technology called Adaptive Spatial Lattice Manufacturing (ASLM). Through a fabrication process involving an AI program and hardware, the start-up enables industrial manufacturers to create large lattice structures at scale. A breakthrough in engineering as this meshing of metal rods welded together is 70% lighter than parts made out of metal sheets.
Tetmet develops machine learning software that guides robotic arms and laser beams, can be used on standard equipment, and integrated into pre-existing toolchains. Part of the protocol also includes mini cameras that feed the program with images from different angles, so it can deliver a sharp precision when building parts, and adjust parameters for thermal tuning or vibration filtering.
The technology adapts to the type of metal rods used to build the lattice structures, which is essentially steel and aluminium so far. “Basic metals that are easy to recycle and can be part of a circular model.”, says Tom Vroemen, stating it would prevent industrials from using rare, expensive composites and polymers. Now in the middle of a research and development phase, the start-up envisions a custom-based approach to enable their technology for their customers, whether by commercializing the software only or producing parts in-house. “We dedicate 50% of our efforts to putting together an entire value chain for ASLM.”
From car to satellite
Working with clients like Safran on new plane seat legs or Ariane, Tetmet is currently having samples tested in the aviation, automotive, and space industries. The start-up also signed a program with Stellantis to design the manufacturer’s future cars. “We have a four-million agenda for 2025”, says Tom Vroemen. Lighter structure on satellites also means less fuel and money. An essential point at a time when France’s strong industrial arsenal is directly competiting against giants like SpaceX…
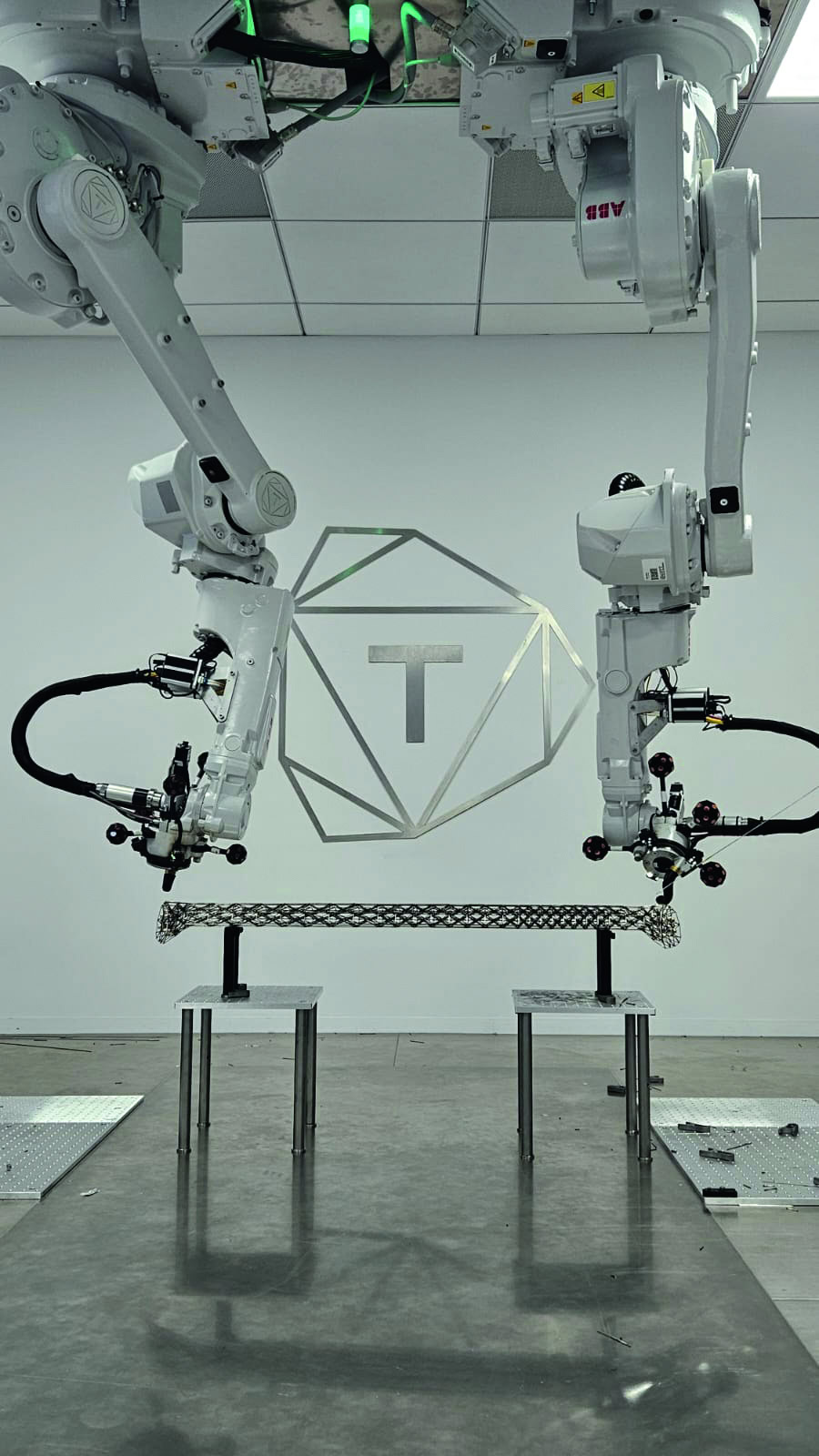

Published by La rédaction